“勞動強度低了,工作效率高了;人員減少了,回煤生產工效高了;設備堵卡事故率少了,操作簡易方便了;自動化程度高了,裝車輕松便捷了。”山東能源棗礦集團蔣莊煤礦智能化選煤廠在持續推進過程中不斷散發出“青春活力”。
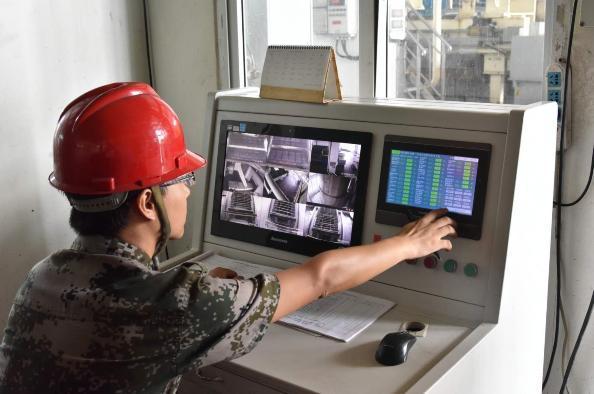
蔣莊煤礦選煤廠持續提升裝備水平和自主創新能力,堅持用人最少、效率最高、效益最優工作思路,不斷優化、完善各生產系統,力促設備提檔升級,逐步向全面智能化不斷推進。“過去一臺壓濾機只有70塊濾板,現在換了新裝備,濾板增加到105塊,處理能力提升了50%,產量由過去的4.5t/循環提升至6.75t/循環,單機日處理量提升85t,極大的緩解煤泥水處理壓力,職工勞動強度大大降低。”該廠洗煤車間主任王義春說。原來,選煤廠針對原壓濾設備老化、工藝落后、洗選效率低等制約生產的“瓶頸”問題,對原使用的壓濾設備進行了更換升級,新型設備自動化循環卸料實現了壓濾機智能控制,職工從崗位操作工轉變為巡檢工,生產效率提高了25%。在洗煤壓濾車間有著10年工作經驗的壓濾工張萍,提起壓濾機的更換升級,對其稱贊滔滔不絕。“在整個壓濾機卸料過程中,我們原來需要人工2個人配合卸料,頻繁開停設備,勞動強度非常大,20分鐘完成后全身都濕透了。如果再遇到煤泥水噴料的情況,現場環境和安全系數更是不可保證。現在我們只需要1個人輕輕按下按鈕,在不靠近設備的情況下5分鐘便可獨立完成卸料,環境變美了,而且安全也有了可靠的保證。”張萍開心的說道。
他們還對回優化升級,先后安裝使用了齒輥篩、破碎機以及除鐵器。“回煤系統的升級改造,徹底解決了外來煤超粒度問題,減少設備堵卡事故率,入洗原煤符合重介分選工藝要求,提高了回煤生產工效,降低職工勞動強度。”該廠裝運車間主任孟祥龍說。針對原來渣漿泵入料中容易進入超粒度顆粒,極易造成堵塞的問題,他們設計制作了渣漿泵除雜裝置。該裝置通過底部放料閥門,讓超粒度顆粒自流卸出,如有超大顆粒物料,可拆卸上部端蓋,提出箅網,清除雜物,防止對泵體內部結構造成破壞。“為徹底解決濃縮機壓耗事故不易被發現的狀況,我們通過技術創新改造,在濃縮機上自行設計安裝了濃縮機停耙報警裝置。”選煤廠機電技術員張建說。據張建介紹,耙式濃縮機是選煤廠煤泥水處理的主要設備,在停止運行的時候,一旦發現不及時,事故會從停耙事故向壓耙事故惡性轉變,增加維修處理難度和勞動強度,嚴重影響洗煤生產的正常運行。目前,該裝置已投入使用,當濃縮機運行停止,接近開關檢測的信號時間差超過設定值,操作室的報警燈就會亮起,調度員可以很直觀的觀察到報警信息,以便及時通知人員對現場設備進行維修處理,避免了生產事故發生,提高了設備的運轉率,具有較好的推廣、應用價值。“今年以來,我們不斷提高裝備水平、優化生產系統和勞動組織,先后對大型設備進行投入安裝使用,并通過創新改造,先后完成了浮選遠程定量加藥、塊矸遠程放倉、地銷裝車遠程控制等一系列自動化系統改造,提高了生產能力和工作效率,降低了職工的勞動強度。”該廠廠長褚衍靜說。
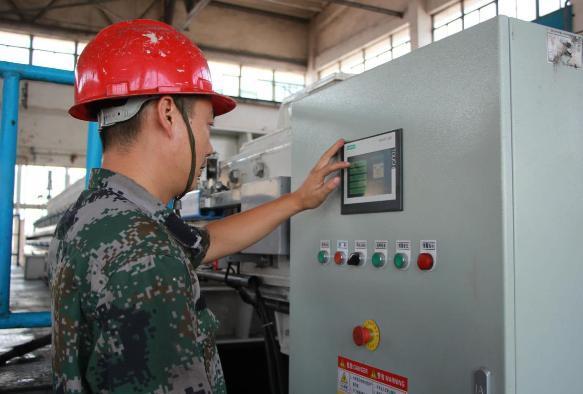
在此基礎上汽車裝車及壓車系統進行了智能化升級改造,該裝置利用皮帶和伸縮溜槽裝載、壓實一次完成,工作人員僅需動動手指進行“一鍵啟動”操作即可節省人力和操作時間,裝車速度由原來的100噸/小時提高到目前的600噸/小時,原來人工裝車至少需要2部鏟車8人輪流操作,現在只需3人即可完成所有工作,解決了精煤直接落地的難題,提高了設備自動化程度、安全系數和裝車效率,為地銷精煤裝車外運帶來極大便捷。并通過封閉式裝車,消除了煤塵污染現象。
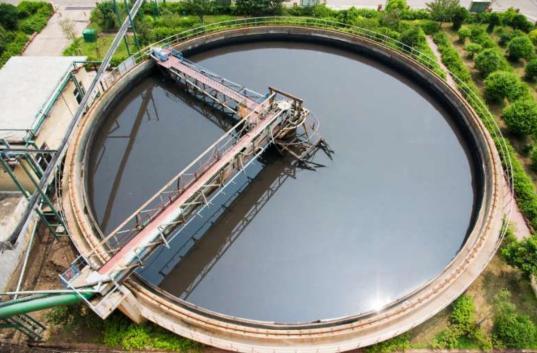
與此同時,他們秉承“小投入、大成效”的理念,投入136萬元進行自動控制系統升級改造,實現了生產系統“一鍵啟停”和全流程自動化控制,可通過視頻監控畫面查看到設備啟動情況。設備在“一鍵啟動”時,集控界面上設備顏色將發生變化,能直觀顯示設備開啟流程,達到了控員提效目的,洗煤生產人員有原170人減至45人,年節約人工成本近千萬元。今年以來,蔣莊煤礦以智能化選煤廠創建為目標,通過實施裝備升級、生產調度集中控制、遠程視頻監控等手段,精簡優化崗位近20個,通過“機械化換人,自動化減人”,實現了控員提效、精干高效。