由于選礦流程設備多、工況復雜,依靠傳統手段實現原料成分、工藝參數、設備狀態和產品質量在線檢測難度很大,這些嚴重制約著選礦流程的精細化控制和資源能源的高效利用。近日,記者在金川集團股份有限公司(以下簡稱金川集團)了解到,金川集團選礦廠利用5G+、AI視覺分析、機器人及智能算法技術,打造了破碎—磨礦—浮選全流程的“數字基礎設施集成”場景,統籌推進選礦數實融合,加快傳統機械化裝備向自動化裝備更新。此前,金川集團選礦廠的“數字基礎設施集成”場景入選了2023年度智能制造優秀場景名單。
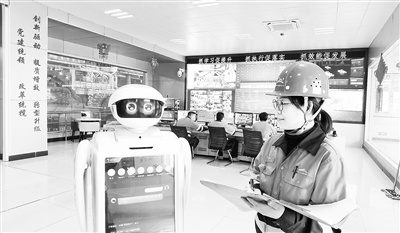
崗位職工向智能巡檢機器人下達指令。 金川集團新聞中心供圖
近年來,全球礦山資源由“高品位、易選別礦種”逐步向“低品位、難處理、多組分共伴生復雜礦為主”轉變。這導致了選礦流程長、資源綜合利用率低、生產成本高等問題,也成為阻礙相關企業結構轉型升級和高質量發展的瓶頸。為解決礦山企業資源高效利用問題,金川集團選礦廠基于選礦工藝的信息化和智能化需求,逐步完成了生產過程中多項應用場景的建設,實現了選礦流程主要工序生產指標、關鍵裝備、人機安全的一體化智能管控。
通過工藝建模、流程仿真、數字化交付等信息化技術,金川集團選礦廠建立了破碎篩分和磨礦分級工藝模型,搭建智能穩定給料場景。“場景的落地不僅打破了碎礦和磨礦工藝參數人工測量、手工調整的歷史,還首次實現了多工序協同控制、參數動態優化和物料平衡,使磨礦可選粒級提高10%以上。”金川集團一選礦車間碎礦生產運行班副班長張金勝說。
針對全區域、各崗位的不同監控需求,金川集團選礦廠基于在線點檢及故障診斷系統搭建設備智能管控場景,增加軌道機器人對浮選設備運行狀態和電機溫度進行實時監測,實現了在主控室和移動端隨時可以查看設備故障診斷與預知性維護信息。由此,設備故障率每年降低約15%。金川集團一選礦車間設備技術員張志揚介紹:“設備智能管控場景通過5G+操控無人化,實現了碎礦全系統‘一鍵啟停’式集中控制,以及原礦段、中細碎段和篩分段的連鎖保護、連鎖啟停。我們在控制系統中組態設置關鍵設備、關鍵測點三區變量和設備運行狀態,實現了關鍵參數的預警和報警。”
應用5G+技術,金川集團選礦廠對底層數據、應用數據進行采集、篩選,將生產運行、設備狀態、安全管控、能源消耗等數據建立成統一數據庫,構建數據智能分析與分層管控、故障自動報警、信息查詢和檢索、數據定期推送等集成化管理,并將集成后的相關數據作為生產信息化管理的指導依據。在“數字基礎設施集成”場景下,2023年,金川集團選礦廠各工序、系統達到了高滿負荷協同作業,全廠系統作業率達到90.7%,部分系統負荷率達到103%,處理礦量達到1250萬噸,同比增加5.84%;鎳回收率完成84.43%,高于計劃0.13%,銅回收率完成78.53%,高于計劃1.03%。
“在數字化選礦建設的道路上,我們積極探索并取得初步效果。但選礦數字化底座還需持續夯實,工藝數據的價值還需深度挖掘,數據治理還任重道遠。”金川集團選礦廠廠長謝杰說。